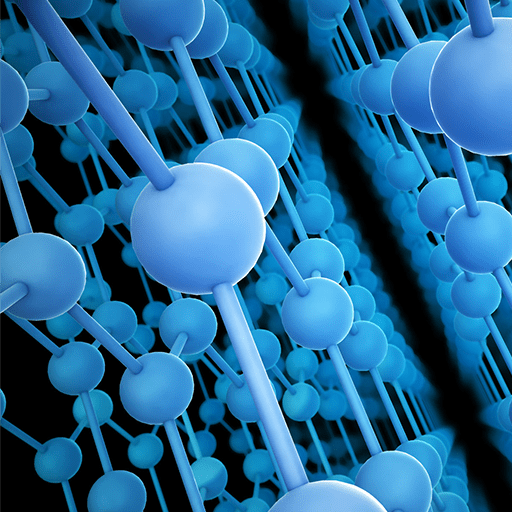
ARL conducts basic and applied research over a broad range of materials, processes and characterization methods. Areas of expertise include metal, ceramic, and polymer additive manufacturing, composites, coatings for corrosion and wear resistance, optics, thermal and environmental barriers, nuclear, biomaterials, gear technology, corrosion, thermo-mechanical processing, high pressure testing, solid-state consolidation and electronic materials and devices.
Modeling capabilities include high strain-rate, design for affordability, large deformation, acoustic tailoring and the impacts of defects on the performance of AM components.
Testing capabilities include corrosion, hot corrosion, wear resistance, oxidation resistance, erosion resistance, mechanical and material properties, optical properties, tribology, vibration and acoustic response. ARL can tailor capabilities to develop material solutions to meet demanding performance requirements.
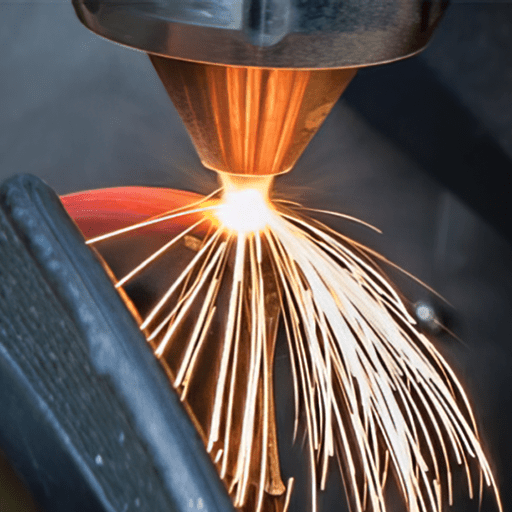
We develop and deploy manufacturing processes and systems to support the current and future needs of our customers product lifecycle management challenges.
We are engaged across the spectrum of manufacturing from trade space design processes, additive manufacturing in metals and advanced coating technologies, to workcell development, through the modeling, simulation and analysis of industrial facilities.
We specialize in developing innovative and affordable technology solutions than can be implemented and sustained by our customers.
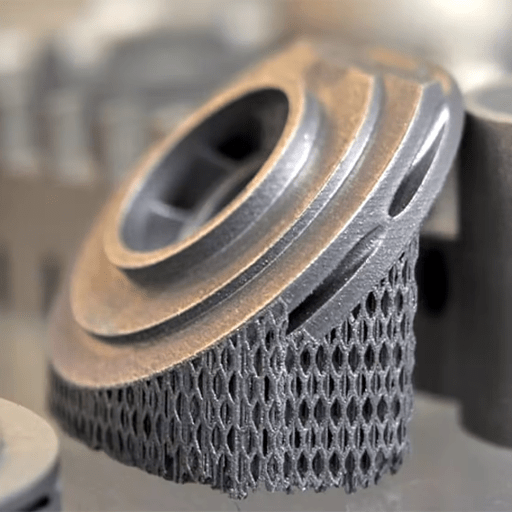
At ARL, effective lifecycle asset management of complex systems starts with conducting reliability engineering and reliability centered maintenance (RCM) assessments to determine the failure modes that have the highest impact on sustainment.
We select the optimum combination of integrated technologies including advanced NDI techniques and Predictive/Prognostic technologies that enable Condition Based Maintenance. Our focus is to enable the most cost effective and advantageous sustainment solutions for your complex systems.
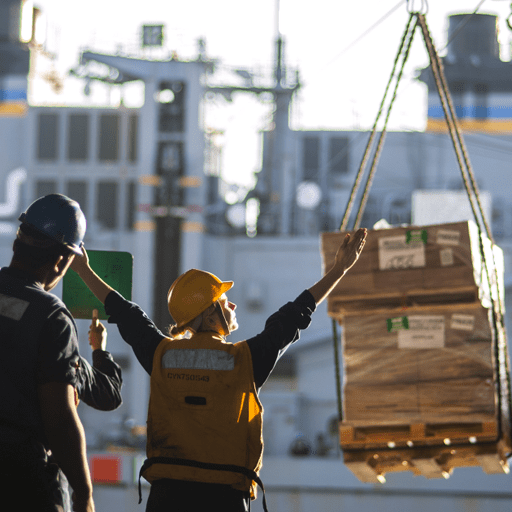
We collaborate with our customers to design solutions that range from the core to the very edge of their enterprises for products including food, water, fuel, equipment, spare parts and medical supplies.
We specialize in conducting supply chain engineering, designing and implementing supply chain systems, and developing specialized expeditionary applications unique to the US military.
WHO WE ARE:
The SOA division consists of the Complex Systems Monitoring Department, Embedded Systems Department, and Vehicle Investigation and Cybersecurity Department that have complimentary missions in the area of lifecycle asset sustainment.
WHAT WE DO:
The unified mission includes:
- We conduct systems analyses to determine the requirements for technologies that enable data driven decision making through the implementation of automated information management, data assurance, machine learning based asset health monitoring, and asset/fleet life cycle management.
- We design and develop prototype hardware/software technologies for autonomous operations, asset life cycle management, and cybersecurity of complex systems using embedded sensors, data collection, control systems, and advanced on-platform and enterprise level data analysis solutions.
- We integrate, test, evaluate, and transition prototype embedded data collection, processing, and control technologies through simulations in the laboratory and with application to full-scale physical assets in field environments.
Capabilities include:
- Embedded System Development and Platform Technology Integration
- Robotic Technology Development and Autonomous Intelligent Systems
- System Analysis including Reliability Centered Maintenance and Cost Benefit Analysis
- Health Monitoring System Design including Diagnostic and Prognostic Algorithm Development
- Vehicle Fleet Life-Cycle Management
- Advanced DoD Vehicle/Platform Technologies
- Utilization of Digital Networks for Health Management and Cybersecurity of Military Platforms
- Integrated System Prototypes including Technologies for Ground Vehicles, Naval Systems, and Expeditionary Fuel Systems.
WHY IT MATTERS:
Our goal is enabling our customers to leverage advanced technologies to become data driven decision makers for the sustainment of their critical assets.
WHO WE ARE:
An interdisciplinary group of engineers, software developers, functional business process experts, and IT professionals who collaborate to support effective and efficient digital transformation programs.
We conduct basic and applied R&D efforts focused on acquiring data, turning data into information and knowledge, and delivering that data, information, and knowledge to the right warfighter at the right time.
Our research spans the spectrum from the tip of the spear to the heart of the enterprise.
WHAT WE DO:
- We improve the operational effectiveness, accuracy, and efficiency of logistics support to DoD Components.
- We model and simulate supply chains and analyze the resulting data in order to develop risk-aware optimization policies supporting operational readiness.
- We develop blockchain applications for permission management in low-bandwidth environments and trusted-asset-condition.
- We develop mesh network technology for asset tracking and low-bandwidth data transmission.
- We conduct data modeling and data engineering supporting applications ranging from enterprise resource planning to machine learning pipelines.
- We develop machine learning applications to predict future supply chain and logistics events and performance.
- We improve the operational effectiveness and efficiency of the DoD enterprise logistics systems.
- We optimize and refine best practices associated with the DoD’s enterprise computing systems.
- We help our customers reduce dependency on expensive and cumbersome customizations in order to gain more efficiency and reduce sustainment cost of these large IT investments.
- We prototype and demonstrate emerging capabilities and technologies associated with enterprise systems so that our customers can better understand how to leverage these tools in their organizations.
- We challenge and educate our customers to consider business process changes in concert with technology implementations to holistically improve their organizational performance.
- We collect data via user-facing applications and sensor integration.
- We develop architectures to move, manipulate, and learn from that data.
- We provide intuitive decision support tools to end users such as:
- Hands-Free Electronic Health Record Initiative – We developed a Microsoft HoloLens based tool that allows battlefield medical providers to: enter critical medical information via verbal input, freeing their hands to continue treating the patient; see critical information about the patient without diverting attention away from the patient; and understand their placement on the battlefield and the nearby threats and resources.
- USMC Tactical Service Oriented Architecture (TSOA) – We built messaging and management infrastructure for the Marine Corps’ TSOA. This includes publish/subscribe messaging, standardized APIs via Remote Procedure Calls, message validation, user authentication and management, data storage, system monitoring and control, and a suite of administrative and development tools. TSOA leverages a node-based architecture with data federation to share information throughout the battlespace. Each node can operate independently and provides a shared data environment so that new applications and services can be quickly developed to utilize existing data. This system has successfully transitioned and fielded to Combat Operations Centers (COC) throughout the Marine Corps.
WHY IT MATTERS:
Our customers face the challenge of operating the world’s most complex organizations in the world’s most complex environments and the tools they use must speed decision making to outperform their competitors. They benefit from ARL’s targeted research to support decisions that help them improve the effectiveness and efficiency of their operations.
WHO WE ARE:
The Materials Science Division consists of:
- Metals, Ceramics, and Coatings Processing Department,
- Electronic Materials and Devices Department,
- Material Engineering and Evaluation Department,
- the Process, Physics, Analytics and Engineering Department,
- Center for Innovative Metal Deposition Processes through Direct Digital Deposition (CIMP-3D),
- Drivetrain Technology Center which includes the Gear Research Institute (GRI) and the High Pressure Test Facility.
Division faculty and staff support the development and implementation of material and material related solutions.
WHAT WE DO:
The mission includes:
- Developing long-term strategic relationships with sponsors to support development and transition of key technologies to meet critical mission requirements.
- Basic and applied research to:
- Develop new materials and material processes;
- Increase capabilities of existing materials and material processes;
- Material testing and characterization;
- Develop and test prototypes;
- Transition technology and provide materials and manufacturing expertise.
- Develop advanced materials and process existing and emerging applications. Specific areas include metal and ceramic additive manufacturing, coatings, electronic and optical materials, sensors and electronic devices, gears, solid-state consolidation and hybrid materials.
- Develop and implement material models, sensors and characterization methods for in-situ process monitoring modeling, development of process-property relationships and optimization of materials and material processes.
- Transition materials and repair technology including process specifications for vendors, training, qualification requirements and support.
WHY IT MATTERS:
Our goal to develop optimal solutions to material and material related issues to enable our customers to solve current and emerging problems and to provide subject matter experts for material issues.
WHO WE ARE:
The Manufacturing Systems Division consists of the Product and Process Design Department, the Lifecycle Engineering Department, and the Production Engineering Department.
WHAT WE DO:
- We continue to develop lines of basic research in:
- Design methods
- Additive manufacturing
- Process planning
- Artificial Intelligence with focus on design, manufacturing, and systems engineering
- UAS sciences (aero, control, sensors)
- Transition results of basic research into direct support for our government sponsors.
- Support internal lab processes from manufacturing to systems engineering, including:
- Improving ARL’s ability to execute its programs
- Using ARL as a sandbox for process improvement
- Very rapidly conceive, reduce to practice, and deploy systems for operational support and sustainment.
- Running a “skunkworks” focused on sustainment technologies
- Serving as a template for other organizations developing their own rapid response
- We conduct unmanned air systems research and operations.
- MSD owns 3 of 6 standardization pilots for the University
- Private airfield for flight test provides unique capability
- We grow our nation’s future leaders in the areas of design and manufacturing.
WHY IT MATTERS:
Design and manufacturing is where ideas are reduced to practice. Our nation’s competitiveness is directly tied to our capability in these domains.
WHO WE ARE:
The Electro-Optics and Electronics Division provides trusted agent services; industry interface; research and development; modeling and simulation; system design, fabrication, integration, testing & evaluation; and acts as a repository of knowledge for the US Navy, and other Department of Defense (DoD) entities in technical areas related to electro-optics & electronics.
Our work with industry, academia professional organizations and government laboratories serves to nurture the development of electro-optic and electronic materials/components, and transition successful technologies needed for the advancement of the nation’s defense capabilities.
Intimately tied to our designation by the Office of Naval Research (ONR) as a Manufacturing Technology (ManTech) Center of Excellence in Electro-Optics (since 1999) and Electronics (since 2021), we rapidly and nimbly develop solutions to reduce the acquisition costs of US Navy platforms through improved manufacturing processes, introduction of emerging technologies, and technology transfer between the commercial and military market sectors.
WHAT WE DO:
- Advance the state of the art for optical sensors, software and systems for the U.S. Navy and other DoD service and agency customers
- Support the design, development, integration, testing and transition of high energy laser systems, subsystems and components
- Design and deliver integrated optical and mechanical solutions for complex optical systems
- Provide an accessible and agile competency in fiber optics and photonics, sensitive to the needs of the US Navy and the US government
- Maintain a vertically-integrated laboratory with extensive capabilities for R&D, prototyping, reliability, failure analysis and manufacturing technology specializing in electronic, piezoelectric and optical materials
- Develop and transition innovative technology and process solutions to maintain competitive manufacturing technology leadership in issues of national importance
WHY IT MATTERS:
The greatest ongoing challenge facing DoD technology advancement is transcending the “gap” between identifying and developing the most promising research and transitioning it to manufacturing for field and fleet acquisition. Transcending this gap is precisely what we do. From groundbreaking research to extending the lives of legacy systems, our staff has successfully demonstrated we can meet our sponsors’ most challenging technology transition requirements.
By addressing warfighter issues from a systems-focused perspective, we are able to shorten the development life cycle and expediently field relevant solutions at lower cost and greater availability.
WHO WE ARE:
The Materials Design and Optimization Division conducts basic and applied research in composite, multi-material, and multi-functional hybrid materials and structures for DoD and industrial applications with emphasis on performance, reliability, affordability and technology transfer.
WHAT WE DO:
We have expertise across the entire process of creating new, novel composite and multi-functional materials. This expertise includes formulation of the material chemistry, manufacturing, component and system level mechanical design/analysis, and quality assurance through both destructive and non-destructive testing.
Capabilities include:
Fabrication Process Development and Optimization
Fabrication facilities include:
- 3′ diameter x 7′ Baron autoclave with computer control to 250 psi maximum pressure and 825°F maximum temperature processing limits
- Meter/mix equipment with 2 component/solvent flush, heated pots/delivery lines, vacuum degassing and static mixer used for RTM and VARTM processing
- McClean Anderson filament winder with Compositrak control, 4 programmable axes suitable for both prepreg tow and wet winding
- 6′ x 6′ x 10′ curing oven (500°F)
In addition ARL-Penn State maintains a machine shop with 38 stations that include six 5-axis, three 4-axis and four 3-axis CNC machining stations. ARL has access to 0°F walk-in freezers and standalone chest freezers. CMD maintains data acquisition capabilities for a wide range of in-situ process monitoring.
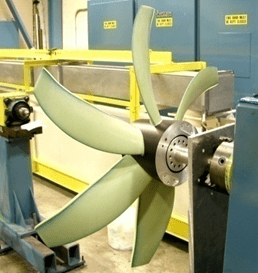
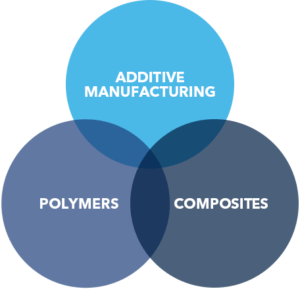
Advanced Manufacturing
We research at the intersections between additive manufacturing, composites, and polymeric materials. We develop processes to enable new functionality using advanced designs of composite materials with selective placement of material properties within complex geometries for more intelligent designs.
This multiple material composite design capability includes process and machine optimization in order to reliably manufacture multi-functional parts for applied end use applications.
WHY IT MATTERS:
With proper design, composite and hybrid materials can provide increased performance through weight savings and increases in specific strength while simultaneously enabling enhanced capabilities through embedded multifunctionality. The Materials Design and Optimization Division has a demonstrated history of creating and transitioning advanced material solutions to our DoD customers and our systems can be found throughout the undersea and surface fleets.
WHO WE ARE:
Penn State’s Center for Innovative Material Processing through Direct Digital Deposition (CIMP-3D) is a University-wide activity that seeks to discover, develop, and deploy additive manufacturing (AM) technology for critical applications. The Center is operated by fulltime Applied Research Laboratory personnel and comprising more than 100 faculty, staff, and students across a broad range of engineering and scientific disciplines. We’re committed to advancing AM science and technology through expertise in AM materials (engineering, characterization, and evaluation), processes (physics, analytics, engineering), and design.
WHAT WE DO:
- We advance the enabling science and technology required to successfully develop, evaluate, and implement additive manufacturing for critical components and structures.
- We provide scientific expertise, technical assistance, and serve as an honest broker to our government (e.g., DoD, DOE, NASA, DARPA) and industrial sponsors through selection, demonstration, and validation of AM technology.
- We promote the potential of AM technology through training, education, and dissemination of information.
CIMP-3D supports both fundamental research and applied development for AM of metals, polymers and ceramics. Our expertise spans all technology readiness levels and all aspects of AM: advanced AM-enabled designs; materials design, modeling, & characterization; process engineering, simulation, and optimization; and AM data management and process qualification. We are experienced in leading, executing, and supporting proprietary and controlled programs that advance and apply AM technology for our sponsors.
WHY IT MATTERS:
Our efforts to advance AM science and technologies enable our customers to improve the performance, capability, and readiness of their critical, engineered assets.
ARL is partnered with a wide range of research facilities, centers, and institutes. Our partnerships help advance the state-of-the-art technology and practices within our many research areas.
Research Facilities
- Additive Manufacturing Laboratory
- Drivetrain Technology Center
- Cold Spray Laboratory
- Composites Laboratory
- High Pressure Test Facility
- High Temp. Coating Laboratory
- Electronic Materials and Devices Laboratory
- Electro-Optics Systems Laboratory
- Field Assisted Sintering Laboratory
- Advanced Logistics Systems Integration Laboratory