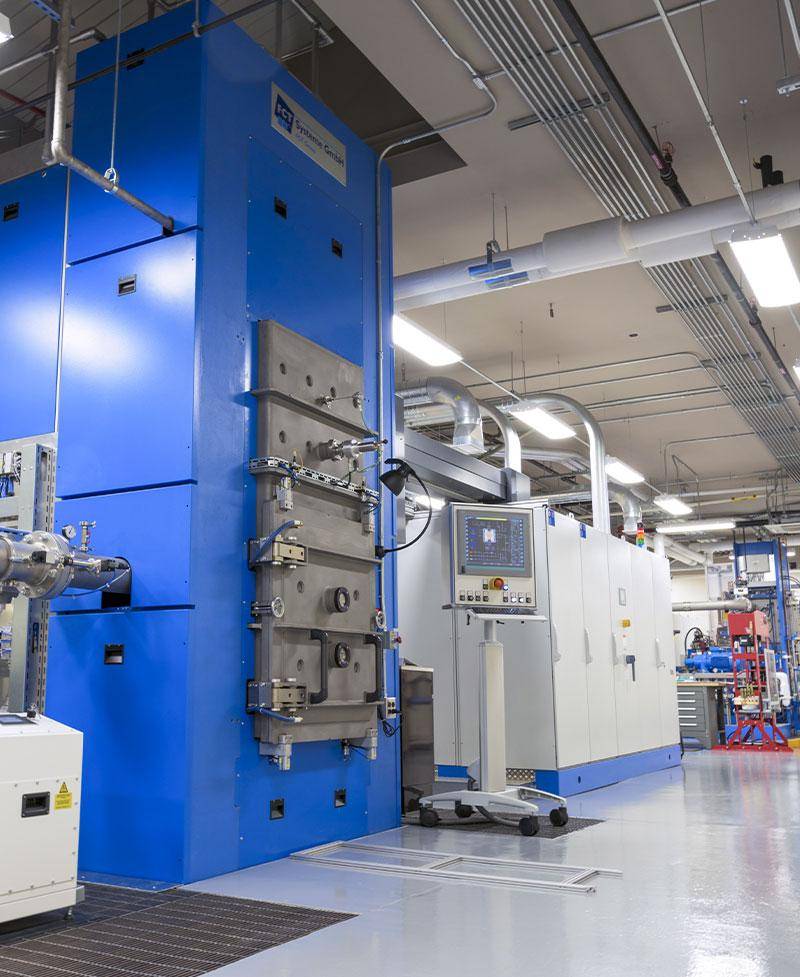
A research facility for joint collaborative research and prototyping
Field Assisted Sintering Technique (FAST) is an emerging manufacturing technology that offers higher heat rates, lower sintering temperature, and faster times than conventional consolidation processes.
FAST has several advantages including fast process times, reduced grain growth (retention of nanoscale features in nanomaterials), high density, and superior physical and mechanical properties. FAST can be used to rapidly sinter metals, ceramics, and composites (including metal matrix composites, and ceramic matrix composites).
Penn State is the only academic institution in the country having three FAST systems with 25, 250 and 325 ton capacities, with maximum operating temperatures of 2200°C. These systems can be used in combination with vacuum systems or back filled with nitrogen or argon gas.
These units allow ARL to manufacture components up to 350mm in diameter (~14 inches) and with heights up to 150mm – 250mm (6-10 inches) depending upon materials. These systems have been used to produce ceramic, metal, and composite material systems include ceramic armor, high thermal conductivity materials, blanks for cutting tools, sputtering and x-ray targets, rocket nozzles and heat sinks.
Benefits of FAST
- High flexibility in processing of materials including functionally graded components
- Processing cycle time: 70-80 times faster than conventional methods
- Theoretical density achievable (up to 100%)
- Effective interface between two dissimilar materials
- Fabrication of net-shaped components
- Retention of nanograined structure
- 20% to 33% less energy consumption than other methods
FAST Applications
- Body Armor Protection
- Ceramic-Metal Joining
- Cutting Tool Industry
- IR - Windows
- Net-shaped Forming Components
- Sensors - MEMS
- Thermal Management - Microelectronics
- Thermo-electric Materials
- Turbine Industry